The Cat fault code list provides valuable diagnostic information when troubleshooting equipment issues. It is essential for identifying problems quickly.
When dealing with heavy machinery or equipment powered by Caterpillar engines, understanding the Cat fault code list is crucial for efficient maintenance and repair. By decoding these fault codes, technicians can pinpoint issues accurately and expedite the troubleshooting process. This comprehensive list categorizes various fault codes related to engine performance, emissions, and system malfunctions.
Each code corresponds to a specific problem, allowing technicians to diagnose and address issues promptly. Familiarizing yourself with the Cat fault code list is essential for ensuring optimal performance and minimizing downtime in industrial settings.
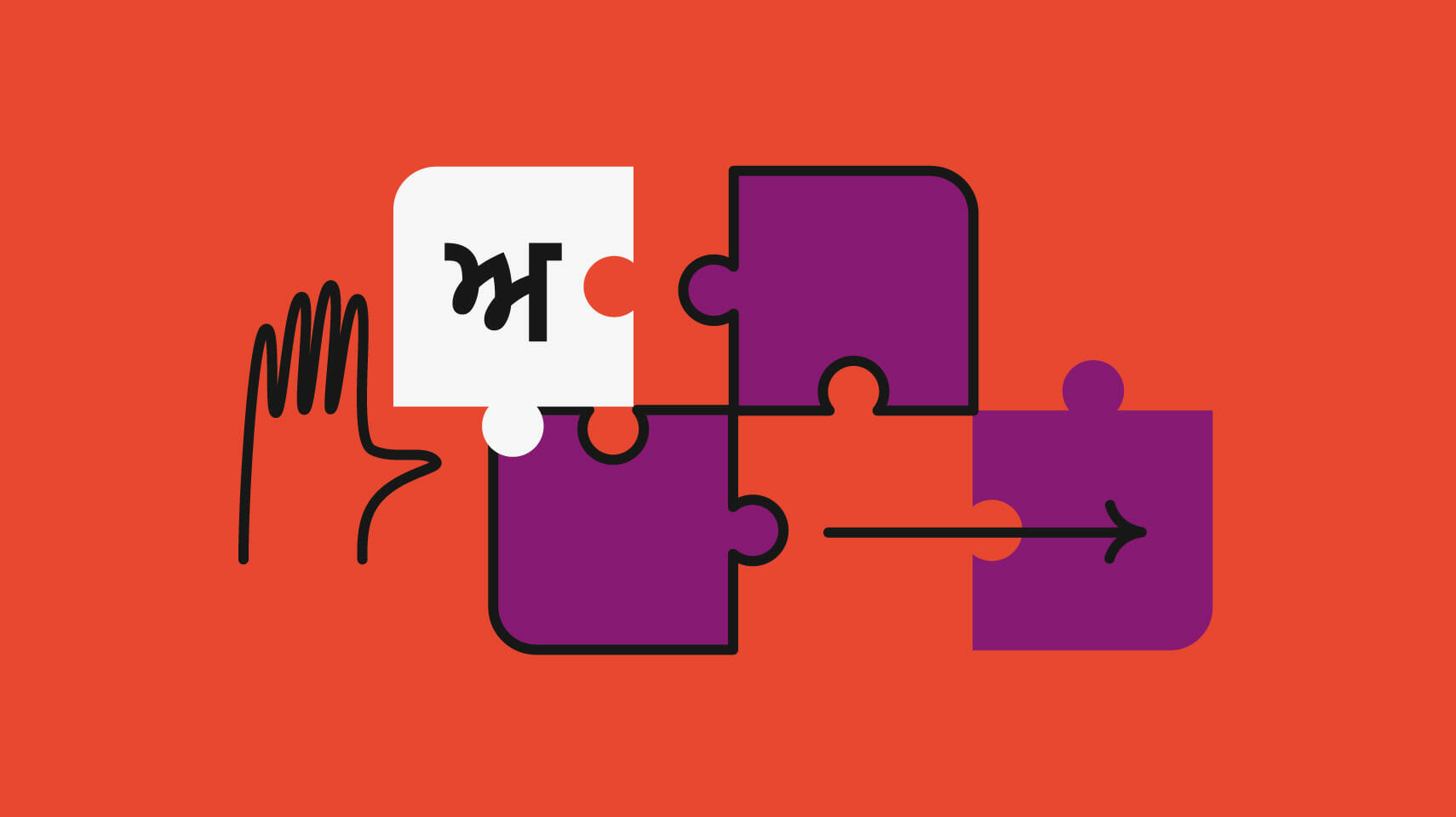
:focal(700x527:701x528)/https://tf-cmsv2-smithsonianmag-media.s3.amazonaws.com/filer_public/54/66/546650fa-26a4-40fd-8d6d-5a7a04540f81/rosetta2.png)
Credit: www.smithsonianmag.com
- Common Cat Fault Codes
- Diagnostic Tools For Cat Fault Codes
- Interpreting Cat Fault Codes
- Addressing Common Cat Fault Codes
- Preventive Maintenance To Avoid Cat Fault Codes
- Cat Fault Codes And Emissions Regulations
- Training For Effective Cat Fault Code Management
- Best Practices For Cat Fault Code Troubleshooting
- Frequently Asked Questions On Cat Fault Code List
- Conclusion
Common Cat Fault Codes
If you’ve encountered issues with your Caterpillar equipment, understanding Common Cat Fault Codes can streamline troubleshooting. Explore P-Codes, C-Codes, and U-Codes to decode the issue accurately.
Exploring P-codes
P-Codes, or Powertrain Codes, typically relate to engine and transmission issues. Use P-Codes to pinpoint specific faults for efficient repairs.
Understanding C-codes
C-Codes, or Chassis Codes, focus on vehicle body and electrical system problems. Decode C-Codes to address issues affecting the chassis components.
Deciphering U-codes
U-Codes, or Network Communication Codes, deal with communication errors between control modules. Unravel U-Codes to ensure seamless data exchange within the network.
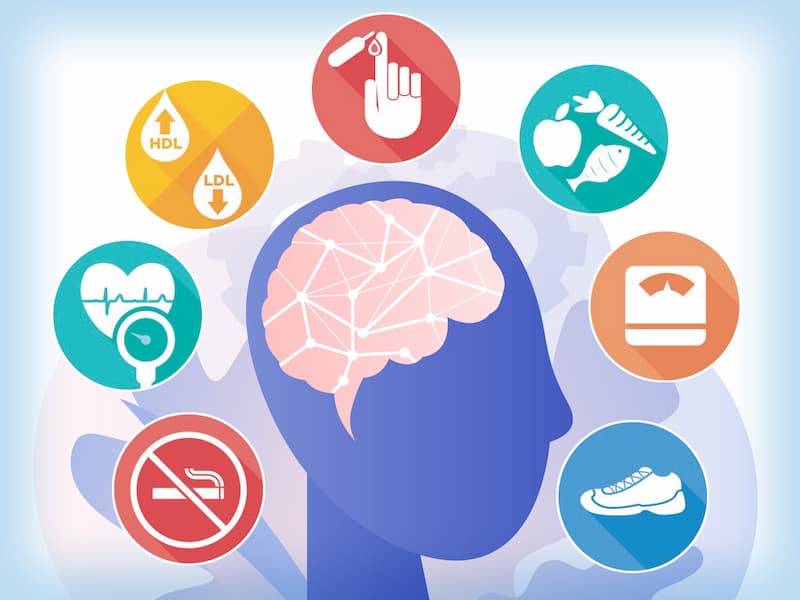
Credit: www.umc.edu
Diagnostic Tools For Cat Fault Codes
Cat fault codes play a crucial role in identifying and resolving issues in Caterpillar equipment. A range of diagnostic tools is available to effectively interpret these codes, enabling quick and accurate troubleshooting.
Obd-ii Scanners
OBD-II scanners are essential tools for retrieving and analyzing Cat fault codes. These scanners plug into the onboard diagnostic port of Cat machinery and provide real-time data on engine performance and system malfunctions.
Cat Et Software
CAT ET software is a comprehensive diagnostic tool that offers advanced capabilities for Cat fault code analysis. It allows users to monitor system parameters, perform diagnostic tests, and access historical data to pinpoint underlying issues.
In-depth Analysis With Cat Electronic Technician
CAT Electronic Technician provides in-depth analysis of Cat fault codes, offering detailed insights into equipment performance and health. This advanced tool enables technicians to diagnose complex problems and implement targeted solutions.
“` By following this HTML format, you can easily integrate this content into a WordPress blog post on Cat fault codes and diagnostic tools.Interpreting Cat Fault Codes
When it comes to diagnosing issues with your Caterpillar equipment, understanding Cat fault codes is crucial. These codes provide valuable insight into the health and performance of your machinery, helping you address problems efficiently and effectively. In this section, we will break down the process of interpreting Cat fault codes, empowering you to make informed decisions and take appropriate action when issues arise.
Identifying System Affected
When encountering a Cat fault code, the first step is to identify the specific system or component that is affected. This information is crucial in determining the appropriate course of action to address the issue. The fault code will often include the system or component name, allowing you to pinpoint the area requiring attention.
Assessing Severity Levels
Each Cat fault code is accompanied by a severity level, indicating the urgency and potential impact of the issue. Understanding these severity levels helps prioritize maintenance tasks and determine whether immediate action is required. By evaluating the severity of the fault code, you can allocate resources effectively and minimize downtime.
Locating The Root Cause
Identifying the root cause of a Cat fault code is essential for implementing lasting solutions. By analyzing the code and conducting thorough diagnostics, you can uncover the underlying issues contributing to the fault. This proactive approach enables you to address the source of the problem, preventing recurring issues and promoting the long-term reliability of your equipment.

Credit: www.pcmag.com
Addressing Common Cat Fault Codes
Cat fault codes can be a frustrating and confusing aspect of owning a Cat machine. These fault codes are designed to help diagnose issues and provide insight into potential problems with your equipment. In this article, we will explore common Cat fault codes and offer solutions to address them, focusing on P-codes, C-codes, and U-codes.
Common Solutions For P-codes
P-codes refer to powertrain-related fault codes, which include issues with the engine, transmission, and drivetrain. These codes often indicate problems that can affect the performance and efficiency of your equipment. Here are some common solutions for P-codes:
- Check the fuel system for any leaks or blockages.
- Inspect the air intake system and ensure it is clean and free from any obstructions.
- Verify the quality and condition of the engine oil and filters.
- Examine the electrical connections and wiring for any loose or damaged components.
- Consider performing a diagnostic test to pinpoint the exact source of the problem.
Typical Fixes For C-codes
C-codes are chassis-related fault codes that pertain to issues with the machine’s body, frame, or hydraulic system. These codes often indicate problems that can impact the overall stability and functionality of the equipment. Here are some typical fixes for C-codes:
- Inspect the hydraulic system for any leaks or damaged components.
- Check the condition of the machine’s tires or tracks and ensure they are properly inflated and aligned.
- Verify the functionality of the braking system and address any issues promptly.
- Inspect the machine’s body and frame for any cracks, dents, or other signs of damage.
- Consider consulting the equipment’s user manual or contacting a Cat technician for further assistance.
Resolving U-codes
U-codes are network-related fault codes that involve communication issues between different electronic control modules within the equipment. These codes can indicate problems with the machine’s sensors, connectors, or wiring. Resolving U-codes often requires a systematic approach and attention to detail. Here are some steps to resolve U-codes:
- Inspect and clean the connectors and wiring harnesses connected to the affected control modules.
- Verify the power supply to the control modules and ensure they are receiving appropriate voltage.
- Check for any physical damage or corrosion on the sensors and connectors.
- Perform an electronic diagnostic test to identify any faulty or malfunctioning components.
- Consider seeking professional assistance if the issue persists or if further troubleshooting is required.
Preventive Maintenance To Avoid Cat Fault Codes
Preventive maintenance is the key to avoiding Cat fault codes and ensuring the smooth operation of your machinery. By implementing a regular maintenance routine, you can significantly reduce the likelihood of encountering these codes and the associated downtime and costs. In this article, we will outline three essential preventive maintenance practices that will help you keep your equipment running at optimal performance levels.
Regular Inspections And Servicing
Regular inspections and servicing are crucial to prevent the occurrence of Cat fault codes. By conducting comprehensive inspections, you can identify potential issues before they escalate into major problems. Inspecting important components such as fluid levels, belts, filters, and wiring ensures their proper functioning and helps to detect any signs of wear and tear. Performing routine servicing, including oil changes, air filter replacements, and lubrication, is essential to maintain the efficiency and longevity of your equipment.
Monitoring Critical Systems
Effectively monitoring critical systems is another vital aspect of preventive maintenance. With the advancements in technology, many Cat machines are equipped with onboard diagnostic systems that constantly monitor various parameters and sensors. These systems generate fault codes when any anomaly is detected, enabling timely intervention and preventive action. Regularly reviewing these fault codes and addressing the underlying issues not only prevents equipment breakdown but also optimizes your machine’s performance and reduces the chances of unplanned downtime.
Proactive Component Replacements
Proactive component replacements form an essential part of preventive maintenance to avoid Cat fault codes. Regularly replacing components that have reached their recommended service life significantly reduces the risk of sudden failures and fault codes. Make sure to adhere to the manufacturer’s recommended maintenance intervals and schedules for specific components. This practice not only ensures the safety of your operators but also extends the lifespan of your equipment, contributes to cost savings, and enhances overall productivity.
Cat Fault Codes And Emissions Regulations
Cat Fault Codes play a critical role in ensuring compliance with emissions regulations, especially in the context of environmental sustainability and regulatory requirements. Understanding the impact of these codes on emissions compliance is essential for businesses seeking to mitigate regulatory risks and ensure environmental compliance.
Impact On Emissions Compliance
The Cat Fault Codes directly impact emissions compliance by providing crucial information about the performance of catalytic converters, diesel particulate filters, and aftertreatment systems. These codes serve as diagnostic tools that help identify issues affecting the emission control equipment, allowing for timely maintenance and repair to maintain compliance with stringent emissions standards.
Ensuring Environmental Compliance
By effectively interpreting and addressing Cat Fault Codes, businesses can actively contribute to environmental compliance efforts. The ability to resolve issues indicated by these codes ensures that emissions from heavy equipment and machinery are kept within permissible limits, thereby reducing the ecological impact and promoting sustainable operational practices.
Mitigating Regulatory Risks
Understanding Cat Fault Codes and promptly addressing related issues is essential for mitigating regulatory risks. Failure to address these fault codes can lead to non-compliance with emissions regulations, resulting in potential legal and financial repercussions. Therefore, proactive management of Cat Fault Codes is crucial for maintaining regulatory compliance and avoiding adverse consequences.
Training For Effective Cat Fault Code Management
Technical Training Programs
Technincal training programs equip professionals with the skills to understand and interpret Cat fault codes.
Hands-on Troubleshooting Workshops
Hands-on workshops provide practical experience in diagnosing and resolving Cat equipment issues related to fault codes.
Continuous Professional Development
Continuous learning ensures professionals are up-to-date with the latest Cat fault code management practices.
Best Practices For Cat Fault Code Troubleshooting
Record-keeping And Documentation
Keep accurate records of all Cat fault codes for efficient troubleshooting.
Collaborative Troubleshooting Approaches
Share information and insights with team members for effective problem-solving.
Utilizing Manufacturer Resources
Refer to Cat manufacturer resources for detailed guidance on fault code resolution.
Frequently Asked Questions On Cat Fault Code List
Q: What Are Common Cat Fault Codes And Their Meanings?
A: Some common cat fault codes include P0420 (Catalyst System Efficiency Below Threshold), P0171 (System Too Lean), and P0300 (Random/Multiple Cylinder Misfire Detected). These codes indicate issues with the car’s catalytic converter, fuel system, or engine performance, respectively.
Q: How Can I Troubleshoot A Cat Fault Code?
A: To troubleshoot a cat fault code, you can start by checking for any loose or damaged connections, inspecting the catalytic converter for signs of damage or clogging, and performing a thorough inspection of the fuel system components. If necessary, it is advised to consult a professional mechanic for further assistance.
Q: Can A Cat Fault Code Cause The Check Engine Light To Come On?
A: Yes, a cat fault code can trigger the check engine light to illuminate. The onboard diagnostics system detects any issues in the vehicle’s systems, including the catalytic converter, and alerts the driver through the check engine light. It is important to address the underlying issue causing the fault code to prevent potential damage to the vehicle’s engine or emissions system.
Q: What Should I Do If I Get A Cat Fault Code?
A: If you get a cat fault code, it is advisable to take your vehicle to a qualified mechanic or dealer for diagnosis and repair. Ignoring the fault code can lead to further damage to your car’s engine or emissions system.
Professional assistance is essential to accurately diagnose and resolve the issue indicated by the fault code.
Conclusion
Understanding and interpreting cat fault codes can be a daunting task, but with the right resources and knowledge, it becomes more manageable. By familiarizing yourself with the common fault codes and their meanings, you can troubleshoot issues more effectively and efficiently.
Implementing the use of a comprehensive cat fault code list can save time and money in the long run, making it an essential tool for any cat owner or mechanic.